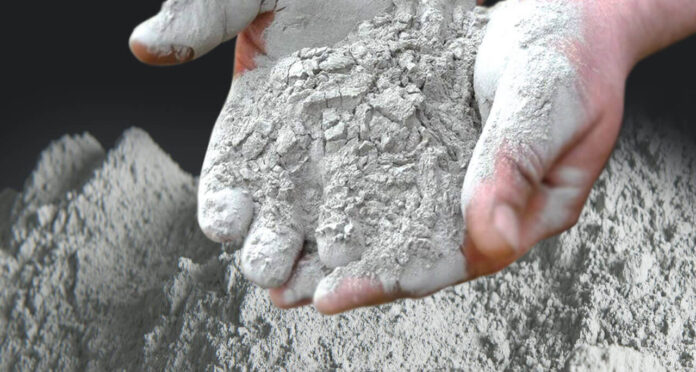
Tính chất của xi măng pooclăng
Tính chất của xi măng pooc lăng
Tham khảo Xi măng Pooc Lăng yêu cầu kỹ thuật TCVN 2682-2009 Xi măng có độ mịn cao sẽ dễ tác dụng với nước, các phản ứng thủy hóa sẽ xảy ra triệt để, tốc độ rắn chắc nhanh, cường độ chịu lực cao. Như vậy độ mịn là một chỉ tiêu đánh giá phẩm chất của xi măng
Khối lượng riêng khối lượng thể tích
Khối lượng riêng của xi măng pooc lăng (không có phụ gia khoáng) ρa = 3,05- 3.15 g/cm3.
Khối lượng thể tích có giá trị dao động khá lớn tùy thuộc vào độ lèn chặt, đối với bột xi măng ở trạng thái xốp tự nhiên ρv = 1100kg/m3, lèn chặt trung bình ρv= 1300 kg/m3, lèn chặt mạnh ρv= 1600kg/m3.
Độ mịn
Xi măng có độ mịn cao sẽ dễ tác dụng với nước, các phản ứng thủy hóa sẽ xảy ra triệt để, tốc độ rắn chắc nhanh, cường độ chịu lực cao. Như vậy độ mịn là một chỉ tiêu đánh giá phẩm chất của xi măng.
Độ mịn có thể xác định bằng cách sàng trên sàng 4900 lỗ/cm2 và đo tỷ diện bề mặt của xi măng.
Theo TCVN 2682 – 1999, khi sàng bằng sàng 4900 lỗ/cm2 thì độ mịn của xi măng thông thường PC30 và PC40 phải đạt chỉ tiêu lượng lọt qua sàng lớn hơn hoặc bằng 85% (lượng sót trên sàng ≤ 15%).
Tỷ diện bề mặt của xi măng là tổng diện tích của các hạt trong 1g xi măng. Xi măng càng mịn tỷ diện càng lớn do đó người ta dùng tỷ diện để biểu thị độ mịn của xi măng.
Cũng theo TCVN 2682-1999 tỷ diện bề mặt của xi măng PC30 và PC40 phải đạt ≥ 2700cm2/g
Hình 4-5: Dụng cụ Vika để xác định độ dẻo tiêu chuẩn
và thời gian đông kết của ximăng
a) Xác định độ dẻo tiêu chuẩn và thời gian bắt đầu đông kết.
b) Xác định thời gian kết thúc đông kết.
Lượng nước tiêu chuẩn
Lượng nước tiêu chuẩn của xi măng là lượng nước tính bằng % so với khối lượng xi măng đảm bảo cho hồ xi măng đạt độ dẻo tiêu chuẩn.
Độ dẻo tiêu chuẩn được xác định bằng dụng cụ vi ka (hình 4 – 5), phương pháp xác định theo TCVN 6017:1995
Hồ xi măng đảm bảo độ cắm sâu của kim vi ka (đường kính kim 10 ± 0,05 mm) từ 33-35mm trong khuôn có đường kính trên 70 ± 5mm, đường kính dưới 80 ± 5mm và chiều cao 40 ± 0,2mm thì hồ đó có độ dẻo tiêu chuẩn và lượng đã nhào trộn là lượng nước tiêu chuẩn.
Lượng nước tiêu chuẩn của xi măng càng lớn thì lượng nước nhào trộn trong bê tông và vữa càng nhiều.
Mỗi loại xi măng có lượng nước tiêu chuẩn nhất định tùy thuộc vào thành phần khoáng vật, độ mịn, hàm lượng phụ gia, thời gian đã lưu kho và điều kiện bảo quản xi măng.
Xi măng để lâu bị vón cục thì lượng nước tiêu chuẩn sẽ giảm.
Cách thực hiện:
Trộn 500g xi măng với một lượng nước đã ước tính sơ bộ.Thời gian trộn kéo dài 5 phút kể từ lúc đổ nước vào xi măng.
Ngay sau khi trộn xong đặt khuôn lên tấm kính, dùng bay xúc hồ xi măng đổ đầy khuôn một lần rồi đập tấm kính lên mặt bàn 5 – 6 cái, dùng dao đã lau ẩm gạt cho hồ bằng miệng khuôn.
Đặt khuôn vào dụng cụ vika, hạ đầu kim (có đường kính 10 ± 0,05 mm và dài 50 ± 1 mm) xuống sát mặt hồ xi măng và vặn vít để giữ kim, sau đó mở vít cho kim tự do cắm vào hồ xi măng. Qua 30 giây vặn chặt vít và đọc trị số kim chỉ trên thước chia độ để biết độ cắm sâu của kim trong hồ xi măng.
Nếu kim cắm cách tấm đế 6±1mm thì hồ xi măng đạt độ dẻo tiêu chuẩn. Nếu kim căm nông hoặc sâu hơn thì phải trộn mẻ khác với lượng nước nhiều hơn hoặc ít hơn. Cứ thí nghiệm nhiều lần như vậy cho đến khi tìm được lượng nước ứng với độ dẻo tiêu chuẩn của hồ xi măng.
Thời gian đông kết của xi măng
Sau khi trộn xi măng với nước, hồ xi măng có tính dẻo cao nhưng sau đó tính dẻo mất dần. Thời gian tính từ lúc trộn xi măng với nước cho đến khi hồ xi măng mất dẻo và bắt đầu có khả năng chịu lực gọi là thời gian đông kết.
Thời gian đông kết của xi măng bao gồm 2 giai đoạn là thời gian bắt đầu đông kết và thời gian kết thúc đông kết.
Thời gian bắt đầu đông kết: Là khoảng thời gian tính từ lúc bắt đầu trộn xi măng với nước cho đến khi hồ xi măng mất tính dẻo, ứng với lúc kim vika nhỏ có đường kính 1,13 ± 0,05 mm lần đầu tiên cắm cách tấm kính 4 ± 1 mm.
Thời gian kết thúc đông kết: Là khoảng thời gian tính từ lúc bắt đầu trộn xi măng với nước cho đến khi trong hồ xi măng hình thành các tinh thể, hồ cứng lại và bắt đầu có khả năng chịu lực, ứng với lúc kim vika có đường kính 1,13 ± 0,05 mm lần đầu tiên cắm sâu vào hồ 0,5 mm.
Thời gian đông kết của xi măng phụ thuộc vào thành phần khoáng, độ mịn, hàm lượng phụ gia, thời gian lưu giữ trong kho và điều kiện bảo quản xi măng.
Các loại xi măng có thời gian đông kết khác nhau. Khi thi công bê tông và vữa cần phải biết thời gian bắt đầu đông kết và thời gian kết thúc đông kết của xi măng để định ra kế hoạch thi công hợp lý.
Khi xi măng bắt đầu đông kết nó mất tính dẻo nên tất cả các khâu vận chuyển, đổ khuôn và đầm chặt bê tông phải tiến hành xong trước khi xi măng bắt đầu đông kết, do đó thời gian bắt đầu đông kết phải đủ dài để kịp thi công.
Khi xi măng kết thúc đông kết là lúc xi măng đạt được cường độ nhất định, do đó thời gian kết thúc đông kết không nên quá dài vì xi măng cứng chậm, ảnh hưởng đến tiến độ thi công.
Từ những ý nghĩa trên mà TCVN 2682 – 1999 đã quy định :
- Thời gian bắt đầu đông kết không được sớm hơn 45 phút.
- Thời gian kết thúc đông kết không quá 375 phút.
Cách xác định: Thời gian đông kết của hồ xi măng được thực hiện theo TCVN 6017: 1995 như sau:
Dụng cụ thí nghiệm là dụng cụ vika (hình 4 – 5) đường kính của kim bằng 1,13 ±0,05 mm.
Trộn hồ xi măng với lượng nước tiêu chuẩn và đổ vào khuôn, giống như khi xác định độ dẻo của tiêu chuẩn của xi măng. Cần ghi lại thời điểm trộn xi măng với nước.
Sau khi cho hồ vào khuôn và đặt trên tấm kính của dụng cụ thì hạ kim xuống sát mặt hồ và vặn chặt vít hãm, sau đó mở vít cho kim tự do cắm vào hồ xi măng. Cứ 10 phút cho kim cắm một lần, khi kim cắm cách đáy 4 ± 1mm thì ghi lại thời điểm đó và tính được thời gian bắt đầu đông kết của hồ xi măng.
Sau đó thay kim nhỏ khác có lắp sẵn vòng nhỏ, đồng thời lật úp khuôn để tiến hành xác định thời gian kết thúc đông kết. Cứ 30 phút cho cắm kim một lần cho đến khi kim chỉ cắm vào hồ xi măng 0,5mm đó chính là thời điểm mà vòng gắn trên kim, lần đầu tiên không còn để lại dấu trên mẫu. Ghi lại thời điểm lúc đó và tính thời gian kết thúc đông kết của hồ xi măng.
Hình 1: Thùng giữ mẫu
Hình 2 :Thùng chưng và luộc mẫu
Tính ổn định thể tích
Xi măng phải đảm bảo tính ổn định thể tích để không bị biến dạng và nứt nẻ, nguyên nhân gây nên hiện tượng không ổn định thể tích là hàm lượng CaO; MgO tự do và khoáng aluminat canxi lớn, các chất này khi khi cứng rắn thường nở thể tích. Mặt khác nếu lượng nước sử dụng nhiều quá cũng gây hiện tượng co cho đá xi măng cũng như bê tông và vữa.
Để xác định tính ổn định thể tích bằng phương pháp mẫu bánh đa theo TCVN 4031:1985 người ta trộn 300g xi măng với nước thành hồ dẻo tiêu chuẩn, chia hồ xi măng thành 4 phần bằng nhau, nặn mỗi phần thành một viên bi, đặt mỗi viên bi lên một tấm kính đã lau bằng dầu nhờn rồi rung tấm kính cho đến khi các viên tạo thành hình tròn dẹt như các bánh đa (bánh tráng) có đường kính 7-8cm, bề dày chỗ giữa chừng 1 cm
Dùng dao ẩm miết từ cạnh vào giữa để mép mẫu mỏng và nhẵn mặt.
Đặt các mẫu đó vào thùng giữ mẫu (hình 4-6) rồi đậy nắp kín và giữ trong 24 ± 2 giờ kể từ lúc tạo mẫu. Sau đó lấy ra khỏi thùng và tách mẫu ra khỏi tấm kính. Đặt 2 mẫu trên lưới thép trên, 2 mẫu trên lưới thép dưới của thùng chưng và luộc mẫu (hình 4-7).
Sau khi xếp mẫu, đun sôi nước trong thùng 4 giờ liền, thời gian từ lúc đun đến lúc sôi không quá 30 – 40 phút. Để mẫu nguội trong thùng đến nhiệt độ trong phòng rồi lấy ra quan sát.
Khi quan sát nếu thấy mẫu thử bị cong vênh và có những vết nứt chạy xuyên tâm ra đến mép thì xi măng được coi không ổn định thể tích (hình 4 – 8).
Nếu các mẫu không bị cong vênh không có vết nứt hoặc chỉ có các chấm nhỏ và một vài vết nứt ở giữa mẫu không chạy ra đến mép, thì xi măng được coi là có tính ổn định thể tích ( hình 2)
Hình 1: Mẫu xi măng ổn định thể tích
Hình 2: Mẫu xi măng không ổn định thể tích
Ngoài phương pháp xác định tính ổn định thể tích bằng mẫu bánh đa còn có thể đo độ ổn định thể tích bằng phương pháp Lơsatơlie theo TCVN 6016:1995. Dụng cụ Lơsatơlie (hình 4 -10) có khuôn bằng đồng đàn hồi có càng đo.
Để xác định độ ổn định bằng phương pháp này cần chế tạo hồ xi măng có độ dẻo tiêu chuẩn rồi cho vào khuôn đã được lau dầu, gạt bằng mặt hồ rồi đậy khuôn bằng đĩa thuỷ tinh (cũng được quét dầu). Cho ngay khuôn vào buồng ẩm, giữ trong 24 ±0,5 giờ ở độ ẩm không nhỏ hơn 98% và nhiệt độ 27 ±1oC rồi đo khoảng cách A giữa các đầu chóp của càng khuôn.
Giữ khuôn ngập trong nước, đun dần đến sôi trong suốt 30 ± 5 phút và duy trì nhiệt độ sôi trong 3 giờ ± 5 phút. Để khuôn nguội đến 27 ± 2oC rồi đo khoảng cách B giữa các đầu chóp của càng khuôn. Hiệu số B – A (mm) chính là độ ổn định thể tích.
Sự tỏa nhiệt
Khi nhào trộn với nước hồ xi măng tỏa ra một lượng nhiệt nhất định, lượng nhiệt đó phụ thuộc vào thành phần khoáng vật, độ mịn của xi măng và hàm lượng thạch cao.
Lượng nhiệt tỏa ra khi thủy hoá của xi măng có lợi trong trường hợp thi công các kết cấu bê tông mỏng, nhỏ vào mùa lạnh vì lượng nhiệt đó sẽ làm cho bê tông rắn nhanh, nhưng không có lợi khi thi công các kết cấu bê tông khối lớn trong điều kiện nhiệt độ môi trường thấp, vì chúng dễ gây rạn nứt cho công trình do chênh lệch nhiệt độ giữa bề mặt và trong lòng khối bê tông. Vì vậy đối với những công trình bêtông khối lớn phải chú ý đến kỹ thuật thi công phân đoạn, mặt khác nếu cần thiết phải dùng loại xi măng có hàm lượng thành phần khoáng C3S và C3A thấp vì đây là 2 loại khoáng có lượng nhiệt tỏa ra nhiều nhất.
Cường độ chịu lực và mác của xi măng
Khái niệm: Xi măng thường dùng để chế tạo bê tông, vữa và nhiều loại vật liệu đá nhân tạo khác. Trong kết cấu bê tông, vữa và vật liệu đá nhân tạo sử dụng xi măng, chúng có thể chịu nén, chịu uốn. Cường độ chịu nén và chịu uốn của vữa xi măng càng cao thì cường độ nén và uốn của bê tông cũng càng lớn.
Giới hạn cường độ uốn và nén của vữa xi măng được dùng làm cơ sở để xác định mác xi măng và mác xi măng là chỉ tiêu cần thiết khi tính thành phần cấp phối bê tông và vữa.
Theo TCVN 6016-1995, mác của xi măng được xác định theo cường độ chịu uốn của các mẫu hình dầm kích thước 40 x 40 x 160 mm và cường độ chịu nén của các nửa mẫu hình dầm sau khi uốn, các mẫu thí nghiệm này được bảo dưỡng trong điều kiện tiêu chuẩn (1 ngày trong khuôn ở môi trường nhiệt độ 27±1°C, độ ẩm không nhỏ hơn 90%, 27 ngày sau trong nước ở nhiệt độ 27±1°C).
Theo cường độ chịu lực, xi măng pooc lăng gồm các mác sau: PC30; PC40; PC50.
Trong đó : PC : Ký hiệu cho xi măng pooc lăng.
Các trị số 30; 40; 50 là giới hạn bền nén sau 28 ngày tính bằng N/mm2, xác định theo TCVN 6016-1995.
Trong quá trình vận chuyển và cất giữ, xi măng hút ẩm dần dần vón cục, cường độ giảm đi, do đó trước khi sử dụng xi măng nhất thiết phải thử lại cường độ và sử dụng xi măng theo kết quả kiểm tra chứ không dựa vào mác ghi trên bao.
Phương pháp xác định :
Mác xi măng được xác định theo tiêu chuẩn TCVN 6016-1995 là phương pháp dẻo (phương pháp mềm).
Muốn xác định cường độ nén và uốn của xi măng phải đúc các mẫu thử hình lăng trụ tiêu chuẩn (dầm) 40 x 40 x 160 mm bằng vữa xi măng cát với tỷ lệ 1:3 theo khối lượng. Tỷ lệ nước/xi măng bằng 0,5.
Dùng các khuôn tiêu chuẩn bằng thép đúc 3 mẫu, gạt bằng và miết phẳng bề mặt các mẫu, đặt các khuôn mẫu đó vào thùng giữ ẩm sau 24 ± 2 giờ thì tháo khuôn lấy mẫu ra ngâm vào nước, thể tích nước chứa trong thùng phải bằng 4 lần thể tích các mẫu thử và mực nước phải cao hơn mặt mẫu tối thiểu 5cm, thỉnh thoảng thêm nước để mực nước không đổi, 27 ngày thì lấy mẫu ra khỏi thùng nước, lau khô mặt mẫu rồi thử cường độ ngay không để chậm quá 30 phút.
Xác định cường độ chịu uốn của mẫu thử như sau:
Đặt mẫu trên 2 gối tựa của máy thí nghiệm uốn theo sơ đồ (hình 3 ).
Hình 3: Sơ đồ đặt mẫu uốn
Sau khi uốn gãy các mẫu, lấy các nửa mẫu đem thử cường độ nén như sơ đồ (hình 4).
Hình 4: Sơ đồ đặt mẫu nén
Diện tích mặt chịu nén F là 16 cm2.
Giới hạn cường độ chịu nén của vữa xi măng là trị số trung bình của 6 kết quả thí nghiệm .
Từ giới hạn cường độ chịu nén và uốn của vữa xi măng tìm được, xác định mác xi măng bằng cách so sánh cường độ với các loại mác xi măng quy định. Ví dụ cường độ nén trung bình của nhóm mẫu xi măng sau khi thí nghiệm là 34N/mm2 vậy xi măng này thuộc loại PC 30.
Ngoài phương pháp dẻo để xác định mác của xi măng như trên còn có thể dùng phương pháp khô (cứng) với các mẫu hình lập phương cạnh 7,07 cm và phương pháp thử nhanh với các mẫu 2 x 2 x 2 cm.
Nhưng hiện nay các loại xi măng của nước ta đều dùng phương pháp dẻo để xác định mác theo đúng tiêu chuẩn của nhà nước quy định.
Các yếu tố ảnh hưởng đến cường độ chịu lực của xi măng :
Cường độ chịu lực của xi măng phát triển không đều, trong 3 ngày đầu có thể đạt 40-50%; 7 ngày đạt 60-70%, những ngày sau tốc độ tăng cường độ chậm đi, đến 28 ngày đạt cường độ chuẩn. Tuy nhiên trong những điều kiện thuận lợi sự rắn chắc của nó có thể kéo dài vài tháng và thậm chí hàng năm, cường độ cuối cùng có thể vượt gấp 2 – 3 lần cường độ 28 ngày.
Cường độ của đá xi măng và tốc độ cứng rắn của nó phụ thuộc vào thành phần khoáng của clinke, độ mịn của xi măng, độ ẩm và nhiệt độ của môi trường, thời gian bảo quản xi măng.
Thành phần khoáng: Tốc độ phát triển cường độ của các khoáng rất khác nhau (hình 4 – 13) .
C3S có tốc độ nhanh nhất, sau 7 ngày nó đạt đến 70% cường độ 28 ngày, sau đó thì chậm lại. Trong thời kỳ đầu (đến tuổi 28 ngày) C2S có tốc độ phát triển cường độ chậm nhưng thời kỳ sau tốc độ này tăng lên và có thể vượt xa cường độ của C3S.
Khoáng C3A là loại khoáng có cường độ thấp nhưng lại phát triển rất nhanh ở thời kỳ đầu.
Độ mịn tăng thì cường độ của đá xi măng cũng tăng vì mức độ thủy hóa của các hạt xi măng được tăng lên.
Độ ẩm và nhiệt độ môi trường rắn chắc có
ảnh hưởng đến quá trình rắn chắc của đá xi măng vì giai đoạn đầu của quá trình rắn chắc là thủy hóa, mặt khác quá trình thuỷ hoá cũng là quá trình xảy ra lâu dài.
Để tạo môi trường ẩm, trong thực tế đã dùng những phương pháp khác nhau như tưới nước, phủ kết cấu bêtông bằng mùn cưa, phoi bào hay cát ẩm, v.v…
Thời gian bảo quản xi măng trong kho càng dài thì cường độ của đá xi măng càng giảm đi dù có bảo quản trong điều kiện tốt nhất. Thông thường trong điều kiện khí hậu của nước ta sau 3 tháng cường độ giảm đi 15 – 20%, sau một năm giảm đi 30 – 40%.
Khi độ mịn của xi măng càng lớn thì cường độ của đá xi măng càng giảm nếu để dự trữ lâu. Vì độ mịn cao làm cho xi măng dễ hút ẩm hơn.
Khả năng chống ăn mòn của đá xi măng
Nguyên nhân
Đá xi măng là loại vật liệu có cường độ chịu lực cao, khá bền vững trong môi trường, tuy nhiên sau một thời gian sử dụng đá xi măng thường bị ăn mòn làm giảm chất lượng của công trình.
Đá xi măng bị ăn mòn chủ yếu là do sự tác dụng của các chất khí và chất lỏng lên các bộ phận cấu thành xi măng đã rắn chắc (chủ yếu là Ca(OH)2 và 3CaO.Al2O3.6H2O). Trong thực tế có tới hàng chục chất gây ra ăn mòn đá xi măng. Mặc dù các chất gây ăn mòn rất đa dạng, nhưng có thể phân ra 3 nguyên nhân cơ bản sau đây:
Sự phân rã các thành phần của đá xi măng, sự hòa tan và rửa trôi hyđroxit canxi.
Tạo thành các muối dễ tan do hyđroxit canxi và các thành phần khác của đá xi măng tác dụng với các chất xâm thực và sự rửa trôi các muối đó (ăn mòn axit, ăn mòn magiezit).
Sự hình thành những liên kết mới trong các lỗ rỗng có thể tích lớn hơn thể tích của các chất tham gia phản ứng tạo ra ứng suất gây nứt bê tông (ăn mòn sunpho-aluminat).
Các dạng ăn mòn cụ thể :
Ăn mòn hòa tan : Do sự tan của Ca(OH)2 xảy ra nhanh mạnh dưới sự tác dụng của nước mềm (chứa ít các chất tan) như nước ngưng tụ, nước mưa, nước sông, nước đầm lầy. Sau 3 tháng rắn chắc hàm lượng Ca(OH)2 vào khoảng 10 – 15 % (tính theo CaO). Nếu sau khi hòa tan và rửa trôi mà nồng độ Ca(OH)2 giảm xuống thấp hơn 0,11% thì CSH và C3AH6 cũng bị phân hủy. Khi hàm lượng Ca(OH)2 có trong đá xi măng tới15 – 30% thì cường độ của đá xi măng giảm đến 40 – 50%.
Ăn mòn Cacbonic : Xảy ra khi nước có chứa CO2 (ở dạng axit yếu). Lượng CO2 tăng hơn mức bình thường sẽ làm vỡ màng cacbonat để tạo thành bicacbonat axit canxi dễ tan theo phản ứng: CaCO3 + CO2 + H2O = Ca(HCO3)2 .
Ăn mòn axit: Xảy ra trong dung dịch axit, có pH < 7. Axit tự do thường có trong nước thải công nghiệp và cũng có thể được tạo thành từ khí chứa lưu huỳnh trong các buồng đốt, trong không gian của các xí nghiệp công nghiệp, ngoài SO2 còn có thể có các anhyđrit của các axit khác, còn có clo và các hợp chất chứa clo. Khi chúng hòa tan vào nước bám trên bề mặt kết cấu bê tông cốt thép sẽ tạo nên các axit, ví dụ như HCl; H2SO4 axit tác dụng với Ca(OH)2 trong đá xi măng tạo ra những muối tan (CaCl2) , muốn tăng thể tích (CaSO4.2H2O ).
HCl + Ca(OH)2 = CaCl2 + 2H2O .
H2SO4 + Ca(OH)2 = CaSO4.2H2O .
Ngoài ra axit có thể phá hủy cả silicat canxi.
Ăn mòn magie: Gây ra do các loại muối chứa magie trong nước biển, nước ngầm, nước chứa muối khoáng tác dụng với Ca(OH)2 tạo ra các sản phẩm dễ tan (CaCl2; CaSO4.2H2O) hoặc không có khả năng dính kết [Mg(OH)2] :
MgCl2 + Ca(OH)2 = CaCl2 + Mg(OH)2 .
MgSO4 + Ca(OH)2 = CaSO4.2H2O + Mg(OH)2 .
Ăn mòn phân khoáng: Là do nitrat amôn phản ứng với Ca(OH)2 có trong đá xi măng: 2NH4NO3 + Ca(OH)2 + 2H2O = Ca( NO3)2.4H2O + 2NH3 .
Nitrat canxi tan rất nhiều trong nước nên dễ bị rửa trôi. Phân kali gây ra ăn mòn đá xi măng là do làm tăng độ hòa tan của Ca(OH)2. Supephotphat là chất xâm thực mạnh do trong thành phần của nó có chứa Ca(H2PO4)2, thạch cao và cả axit photphoric.
Ăn mòn sunfat: Xảy ra khi hàm lượng sunfat lớn hơn 250mg/l (tính theo ): 3CaO.Al−24SO2O3.6H2O + 3CaSO4 + 25H2O = 3CaO.Al2O3.3CaSO4.31H2O .
Sự hình thành trong các lỗ rỗng đá xi măng loại sản phẩm ít tan etringit với thể tích lớn hơn hai lần sẽ gây áp lực tách lớp bê tông bảo vệ làm cốt thép bị ăn mòn. Ăn mòn sunfat luôn luôn xảy ra đối với công trình ven biển, công trình tiếp xúc với nước thải công nghiệp và nước ngầm.
Nếu trong nước có chứa Na2SO4 thì đầu tiên nó tác dụng với vôi sau đó mới tác dụng etringit: Na2SO4 + Ca(OH)2
Nếu quý khách có bất kỳ câu hỏi nào về sản phẩm hay dịch vụ của Công ty Phương Đông, hãy gửi yêu cầu vào e.mail hoặc gọi điện trực tiếp đến số hotline 0946615840 zalo/viber/Fb. Chúng tôi sẽ cố gắng giải đáp mọi thắc mắc trong thời gian sớm nhất có thể ! Mong giúp được công việc của Quý Khách hàng
Số 22 ngõ 43 Nguyễn Phong Sắc, Dịch Vọng Hậu, Cầu Giấy, Hà Nội, Việt Nam
094.66.15.840
sales@oct.vn